Easton’s Country School and Sts. Peter and Paul High School and Family Life Center. Temple B’Nai Israel. The Shore Regional Health Pavilion in Denton. Aphena Pharma, Dart Containers, and Exelon Corporation.
The easily identifiable Willow Construction logo appears on some of the most prestigious building projects in Talbot County and throughout the Delmarva Peninsula.
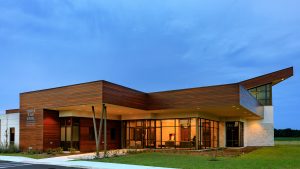
Temple B’Nai Israel, Easton
“There’s not a whole lot of project styles or types of construction we don’t do,” says Andy Cheezum, vice president of operations and senior owner of Willow Construction in Easton, Md. “We’ll try building just about anything.”
Industry Leaders
Over the past 48 years, Willow has become one of the Eastern Shore’s leading construction management firms. While they work on “everything from a $300 job fixing somebody’s door to a $20 million project,” the bulk of Willow’s work is in the healthcare industry, multi-family residential, manufacturing, and other commercial structures. Less than 5% is residential construction and remodeling.
Willow Construction is licensed to work in the state of Virginia, but their primary business footprint runs from the Bay Bridge to Ocean City and in the state of Delaware. The business normally has between 12 and 20 construction projects going on simultaneously which account for between $40 and $50 million in revenue.
“You have to be very diverse if you’re working on the Eastern Shore,” Cheezum notes. “We’re not in a large urban center where we’re building the same building over and over.”
While every project is unique, Willow Construction is fortunate enough to have many repeat customers.
“When we build something, our customers often come back to us to renovate that building,” Cheezum says. “We have built our business on relationships. We see our customers and vendors at the grocery story, at the bank, and at the ballpark. Repeat business is very important for us.”
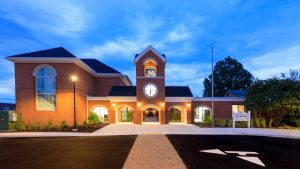
Country School, Easton
A Family Business
Though it was started by Bill Dittman in 1973, senior owners Mike Hiner and Andy Cheezum now lead the company, with Hiner heading up sales and Cheezum managing operations. Rounding out the executive team are Eric Milhollan and Justin Hiner, both junior owners.
“Mike is the ‘get the work’ guy, and I’m the ‘get it done’ guy,” Cheezum explains. “I take what he sells and make it work. It’s a good partnership. I’m not good at what he does, and he wouldn’t sleep at night if he had to do what I do.”
The partners are joined by a team of field supervisors, superintendents, and project managers. All together, the company employees almost 40 people, with another 125 to 200 subcontractors and craft professionals working on projects on any given day.
While they are not technically second generation owners, Willow started as a family business, and Hiner and Cheezum still run it like a family business.
“Mike and I have always said, ‘We’ve got 40 people, but that’s 40 families that are relying on us to make good, sound business decisions so they can get paid on Friday. All of our subs rely on us, and our customers as well. That’s a burden and a challenge.”
Unprecedented and Unpredictable
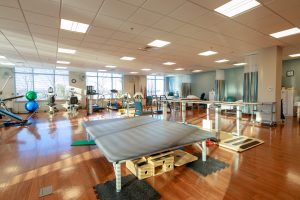
Shore Medical Pavilion, Denton
Of all the challenges that have come their way, COVID-19 has been one the biggest. The construction industry is beginning to feel the after-effects of the pandemic, and Willow is not exempt from these pressures.
“We thought last year is when COVID would negatively impact our business, both from pricing and material availability,” Cheezum says. “The impacts were minor last year. This year? Unprecedented. Unpredictable. We can’t get materials we need.”
On a recent apartment complex project in Worchester County, everything from shingles and drywall to doors and windows were in short supply. Though the team is ready to install the through-the-wall HVAC units now, they aren’t yet in the U.S. They are still on a ship somewhere in the middle of the ocean.
What’s more, the odd winter weather that saw freezing temperatures as far south as Texas has further impacted material availability. The upshot of all of this disruption is that prices are rising, as is the cost of construction.
“Lots of vendors cannot hold their prices for more than five days,” Cheezum explains. “There is serious inflationary pressure, but I hope it is temporary. I am more concerned about what’s it going to be like third quarter of 2022 and maybe 2023.”
Help Wanted
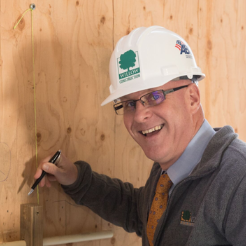
Andy Cheezum, Vice President and Senior Owner
Finding qualified workers is also a universal problem across all industries. “We normally have a very low turnover rate, but I have open positions I have been unable to fill,” Cheezum notes.
Willow typically works as the general contractor for most projects. Most of their employees are professional managers who coordinate and oversee the work of the subcontractors needed for each project.
So what’s the problem? “We just have more open positions than qualified people,” Cheezum says. “That’s how I see it. Most people who would come to work for our team are gainfully employed, and we don’t want to get into stealing staff from our peers.”
The ideal candidate for most of the positions is a recent graduate of a construction management program. Cheezum himself is a graduate of the acclaimed program at the University of Maryland Eastern Shore.
Willow has also been successful recruiting people who have worked “across the bridge” for larger firms, but who are tired of commuting. A good 30% of the current workforce comes from Wicomico and Worcester counties – Berlin, Delmar Fruitland, Ocean Pines, and Princess Anne.
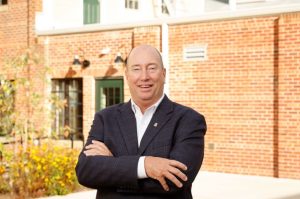
Mike Hiner, President and Senior Owner
Always Looking Ahead
While their list of clients includes some of the most influential businesses on the Delmarva Peninsula, the company is always prospecting for new projects. Because of the time it takes to plan and complete a job, the company books enough work to keep them busy for at least 18 months.
Construction has changed over time, and Willow has changed too. Hiner has been with the company for 40 years, and Cheezum has logged 27, so they’ve both seen a lot.
“The business has become a lot more specialized,” Cheezum says. “We find that we can be more efficient with better pricing if we hire subcontractors who specialize. We’ve got good sound management in the field and in the office to be able to manage projects for our clients.
An Eye on the Future
Though he’s an early riser and is at his desk most days around 5:30 a.m., Cheezum typically doesn’t
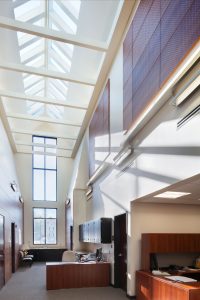
Easton Police Department
take work home with him. Still, the safety of his workers is the one thing that never leaves his mind.
“I work hard, but I leave work at work,” Cheezum explains. “Time and money can fix any problem, except somebody getting injured or killed. Safety is of paramount importance to us. Construction is a dangerous business, and it only takes a second for something to happen.”
Future plans include increasing brand awareness and continuing to grow in their current footprint. The company just moved from its previous office to a new facility on Commerce Drive.
“We like being here in Easton and Talbot County,” Cheezum says. “We do business all over the Delmarva, and we could have moved anywhere. But we chose to stay here.”
For more information, visit WillowConstruction.com.